Pumps play a crucial role in countless industrial applications. Water treatment facilities, petrochemicals, and food companies rely on their continuous operation for productivity and safety. Non-stop work makes these devices prone to wear and tear.
Unexpected equipment failures can be a headache, especially when it involves a critical component like a pump. Such incidents can lead to huge losses due to costly repairs, safety issues, and lost productivity.
With predictive maintenance and machine learning models, however, companies can achieve efficiency while minimizing pump failures. Let’s find out more below.
Table Of Contents 👉
Why Traditional Strategies No Longer Hold
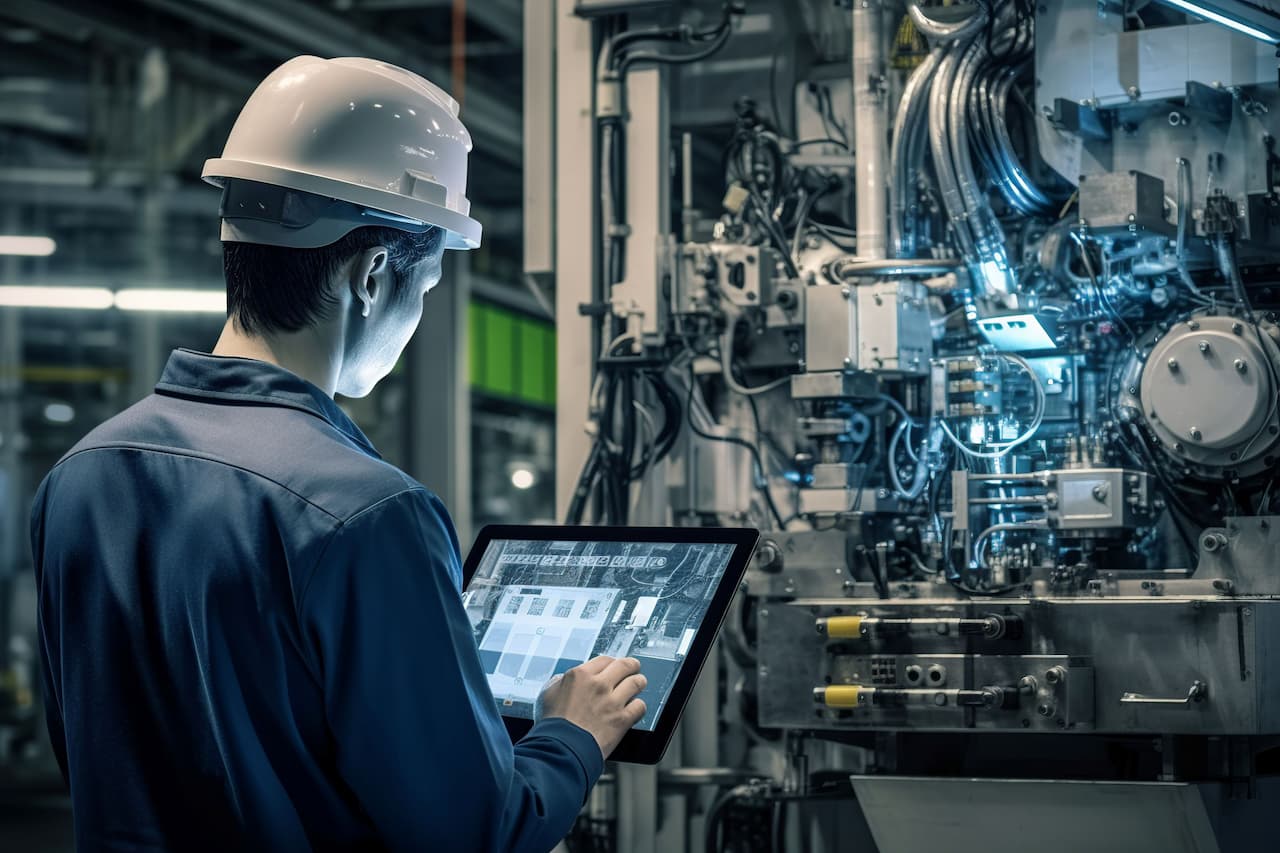
Most people know maintenance activities as either reactive or preventive. In the former, a maintenance team will wait for unexpected failures to happen before performing emergency repairs. Preventive maintenance, on the other hand, focuses on scheduled interventions.
Addressing issues after a failure is disruptive and can lead to higher maintenance costs. Comparatively, performing proactive equipment checks can result in unnecessary maintenance and premature replacement of working parts, which can still hinder operational efficiencies.
Many organizations have switched to a predictive maintenance strategy to keep their operations going. This proactive approach uses machine learning (ML) and predictive analytics to anticipate potential failures and set more reasonable maintenance schedules.
Machine Learning and Predictive Maintenance
Machine learning enables predictive maintenance by analyzing historical data to identify patterns and uncover trends.
Instead of relying on fixed rules, ML models learn from real-time monitoring and readings to detect early warning signs before a pump experiences catastrophic failure.
When upgrading to predictive maintenance technology, companies must ensure equipment performance by purchasing from reliable manufacturers.
Before buying, read through their web pages, for instance, this one from knf.com/en/global and similar supplier sites, to know the benefits and applications of your chosen industrial pumps.
Data Collection and Processing for Pump Maintenance
Machine learning algorithms need a steady stream of high-quality data. Placing smart sensors on centrifugal pumps allows the continuous monitoring of your machine’s actual condition and real-time performance.
It can determine asset performance and spot potential pump failure modes, for example:
A sharp decrease in fluid flow rates could signal blockages, leaks, or impeller wear.
Inconsistent pressure fluctuations can point to pump inefficiency, seal damage, or valve malfunctions.
Abnormal temperature changes could signal problems like lubrication failure, overloading, or restricted cooling flow.
Excessive vibration levels could mean cavitation, bearing problems, abnormal flow passage, or misalignment. These could further damage the connected components.
Predictive maintenance practices involve understanding the connections between different operational metrics and keeping tabs on them.
Thus, apart from vibration sensors, plant managers should consider using the Internet of Things or IoT sensors on critical pieces of equipment that could affect pump performance.
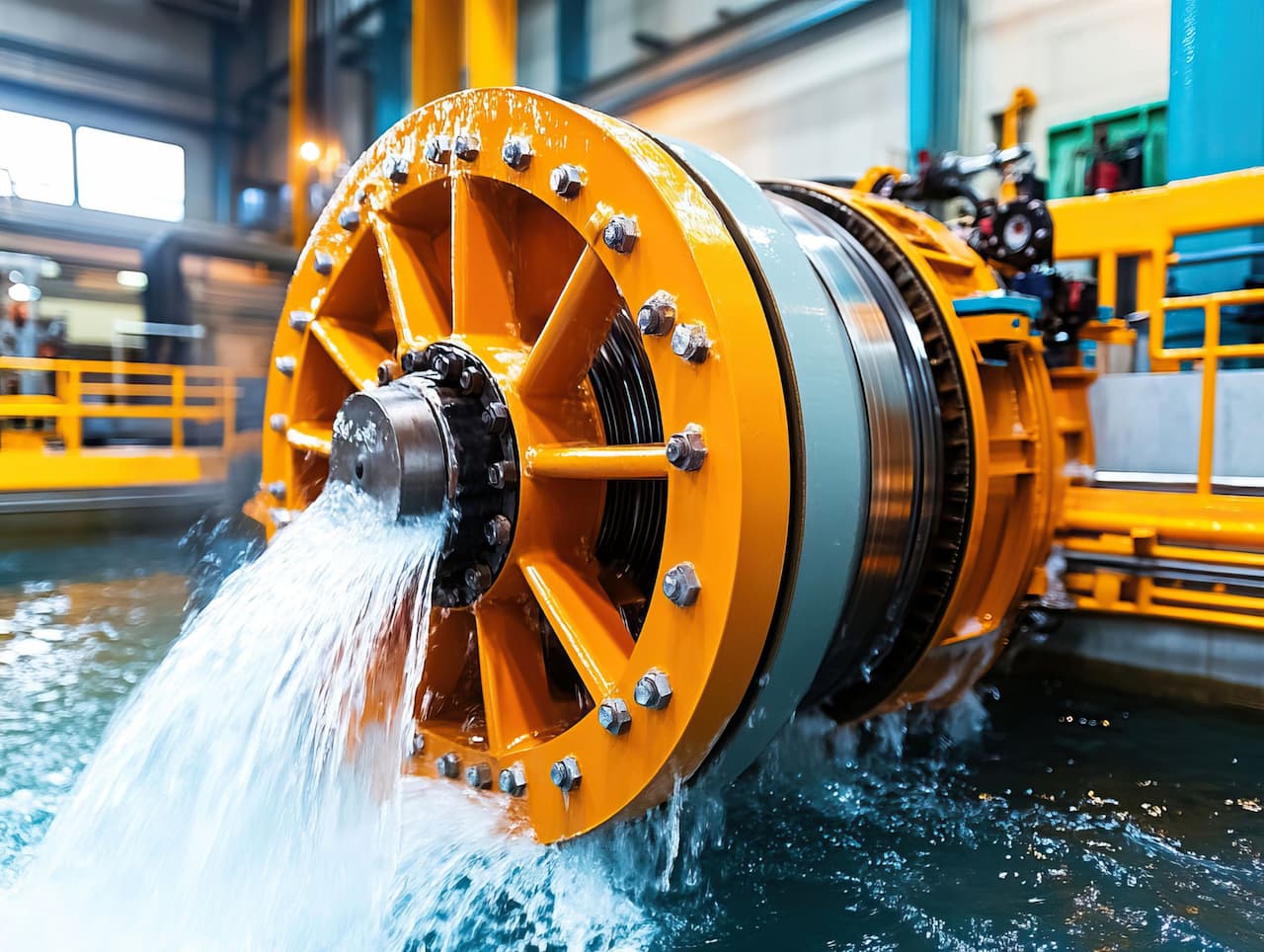
Model Training and Deployment
Training an ML model for predictive maintenance programs involves several steps, the primary tasks being:
Cleaning raw data: Your unprocessed data should be free from inconsistencies and errors to get high-quality output.
Selecting relevant features: Choose the most important variables (i.e., pressure drop, flow rates, vibration levels) you will use to train your predictive maintenance algorithms.
Testing different algorithms: This task evaluates your chosen ML model’s performance in terms of accuracy, robustness, and generalization. For example, a Random Forest algorithm can classify pump conditions, while a deep learning model can detect nuanced patterns in sensor data.
Validation: Choose the metrics that match your goals. Then, perform cross-validation and compare the findings against the results you’ve taken from simple algorithms. You also need to test how well your model processes unseen data, the datasets that weren’t used in your training to see how good it is at generalizing new data and also to prevent bias.
Deployment: After evaluating model performance, decide where you want to run your tool. Cloud infrastructure works great for large-scale analytics.
Manufacturers with distributed digital devices and wireless sensors should consider it. At the same time, edge computing is ideal for real-time data analysis of exclusively on-site devices.
Predictive models work well in potential fault detection. However, catching potential issues shouldn’t be your only concern when implementing predictive maintenance for pumps. Heeding the steps above can help you get started.
Challenges and Limitations
Predictive maintenance isn’t without key challenges, though. Data quality is a common hurdle for most organizations. Faulty sensors and incomplete records can negatively impact the accuracy of the results.
Costs can also be a major concern, especially for smaller businesses. On top of ML model investments, some might need to upgrade their system to accommodate advanced technologies.
More importantly, you must guarantee data privacy and promote transparency and accountability while using the platform.
Final Thoughts
Predictive maintenance addresses the limitations of conventional maintenance approaches. Unlike preventive or reactive maintenance, it allows your systems to pinpoint potential issues with minimal human intervention.
This new approach presents a more cost-effective way to ensure your pumps are in optimal condition and your industrial processes safe and efficient.
While pre-trained models and platforms are available, building your own systems requires technical expertise.
Monitoring systems aside, your operations heavily depend on the reliability of the pumps and pieces of equipment you use. Pick ones that are tested and proven for their performance and longevity.